液压成型机械;液压成型铸匠,塑造金属无限可能
液压成型是一种先进的金属成型技术,利用液压能量将金属坯料塑造成复杂的形状。液压成型铸匠们借助液压成型机械,运用娴熟的技艺和创新思维,为金属加工行业带来了无限的可能性。本文将深入探讨液压成型技术,揭示其原理、优势、应用领域和未来发展趋势。
原理与优势
液压成型是利用高压液体作为动力,通过液压缸和模具对金属坯料施加压力,使其变形并形成所需形状。这种成型方式具有以下优势:
高精度:液压控制系统可精确控制压力和成型过程,确保产品精度和一致性。
复杂性:液压成型可制作形状复杂、尺寸较大的工件,传统工艺难以实现。
材料节省:液压成型过程中,坯料利用率高,材料浪费少。
劳动强度低:液压成型自动化程度高,降低了劳动强度和操作风险。
效率高:液压系统提供了强大的推力和成型速度,提高了生产效率。
应用领域
液压成型技术广泛应用于汽车、航空航天、电子、医疗和建筑等领域。其典型应用包括:
汽车零部件:汽车车身框架、保险杠、车门等
航空航天零件:机翼蒙皮、发动机部件、起落架等
电子元器件:手机外壳、电脑机箱、显示器框架等
医疗器械:手术刀具、假肢、骨科植入物等
建筑钢结构:高层建筑框架、桥梁构件、容器等
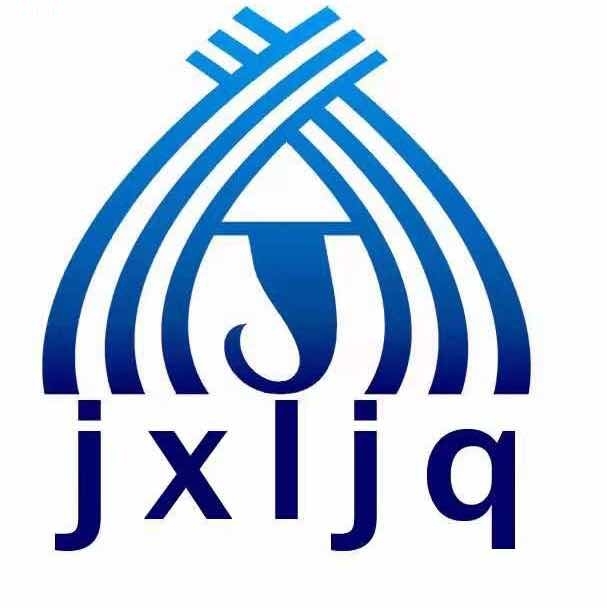
工艺流程
液压成型工艺流程一般包括以下步骤:
1. 设计:根据工件需求设计模具和工艺参数。
2. 制坯:将金属材料裁剪成适当形状和尺寸的坯料。
3. 成型:将坯料放入模具中,施加液压压力进行成型。
4. 冷却:成型后,对工件进行冷却以固定形状。
5. 后处理:根据需要进行修边、去除毛刺等后处理工序。
案例研究
一家汽车制造商采用液压成型技术制造汽车车身框架。通过优化模具设计和成型工艺,实现了高精度、高强度和轻量化的车身结构。与传统焊接工艺相比,液压成型不仅提高了生产效率,还降低了材料成本和劳动强度。
未来趋势
液压成型技术仍在不断发展,未来趋势包括:
复合成型:将复合材料与金属材料结合,实现轻量化和高性能的工件。
增材制造:与增材制造技术相结合,实现复杂结构的快速成型。
智能控制:应用传感器和人工智能,实现过程自动化和产品质量优化。
材料创新:开发高强度、耐腐蚀和热稳定性的新材料,满足不同行业的需求。
绿色制造:采用环保的液体和工艺,减少对环境的影响。
液压成型技术为金属加工行业提供了塑造金属无限可能的强大工具。通过其高精度、复杂成型能力、材料节省和高效率的优势,液压成型铸匠们正在不断突破金属成型的极限。随着技术的不断进步和应用领域的拓展,液压成型技术将在未来继续引领金属加工工业的发展,为各行各业提供创新解决方案。